Imagine a world where your projects run seamlessly, delivering exceptional results with minimal effort and resources. What if you could eliminate inefficiencies, reduce costs, and enhance customer satisfaction all at once? Welcome to the transformative power of Lean principles in project management.
Lean principles for project success focus on maximizing value and minimizing waste throughout the project lifecycle. By applying these principles, project managers can enhance efficiency, improve customer satisfaction, and achieve better project outcomes.
Often associated with manufacturing and process optimization, Lean offers valuable strategies and practices that can be applied to project management, resulting in smoother operations, reduced waste, and increased success rates. In this article, we’ll explore the core concepts of Lean and how they can revolutionize project management.
The Essence of Lean
Lean, initially developed by Toyota in the 1950s as the Toyota Production System (TPS), revolves around
- Eliminating Waste
- Ensuring Smooth and Continuous Flow
- Pursue Perfection through small continuous improvements
To achieve these goals, Lean focuses on three fundamental types of waste:
- Muda
- Mura
- Muri
Muda- Eliminating Waste
In project management, Muda refers to any activity that consumes resources (time, money, effort) without adding value to the project. Recognizing and eliminating Muda is essential for streamlining project workflows. Common sources of Muda in project management include:
- Excessive meetings and paperwork
- Duplication of tasks and efforts
- Waiting time and idle resources
- Overproduction of reports or documentation
Project managers can free up resources, improve productivity, and focus on value-added tasks by identifying and reducing these wasteful activities. Some organizations have process documentation to guide how the work is performed. Sometimes these processes help reduce waste, and sometimes the project will not require these processes, thus amounting to waste.
Mura- Ensuring Smooth Flow
Mura refers to variations or irregularities in work processes that disrupt workflow. These variations can lead to inefficiencies, bottlenecks, and unpredictable project outcomes. To combat Mura in Project Management
- Standardize project processes and workflows
- Balance workloads and allocate resources efficiently
- Use visual management tools like Kanban boards to monitor progress and identify deviations
Project managers can create a smoother project flow by minimizing Mura, making it easier to deliver results predictably and on schedule. The organizational process standards and workflow descriptions can help smooth the workflow.
Muri – Avoiding Overburden
Muri involves overburdening resources or individuals with excessive workloads, leading to burnout, errors, and delays. In project management, Muri can occur when team members are assigned too many tasks or unrealistic deadlines. To address Muri:
- Carefully plan and allocate tasks based on resource capacity
- Implement workload leveling to avoid resource bottlenecks
- Encourage a culture of work-life balance and well-being within the team
Eliminating Muri facilitates smooth flow, prevents team member burnout, and ensures that projects progress steadily and efficiently.
Agile project management approach uses Lean methodology in its workflow. Interested in learning more on Agile. Check out my blog post on Agile principles and mindset here
The Seven Wastes in Project Management
In addition to the Three Ms, Lean also identifies Seven Wastes, also known as the “7 Deadly Wastes.” These are specific categories of waste commonly found in processes.
These seven wastes in the context of Project Management are:
- Transportation
- Inventory
- Motion
- Waiting
- Overproduction
- Overprocessing
- Defects
Transportation: This waste occurs due to communication failures between processes, multiple and complex sources of information, and unnecessary movement of information or materials.
Inventory: Excessive information, inadequate configuration management, complex retrieval systems, and work in progress that is not immediately needed contribute to this waste.
Over Processing: This includes scope creep, unplanned overtime, excessive approvals, overloaded resources, excessive reviews, hand-offs, producing intermediate deliverables, too many iterations, unnecessary data conversions, and excessive verification.
Defects: Rework, poor estimation, conversion errors, inaccurate information, inappropriate design verification, and unclear acceptance criteria are examples of defects that lead to waste.
Motion: Searching for information, required manual intervention, lack of direct access, and no collocation of team members result in wasted motion.
Waiting: Information pushed too early, information unavailable, and periods where no work is being done due to waiting for approvals, supplies, or other dependencies.
Over Production: Producing more than needed, faster than needed, or before it is needed leads to excess production that is not required and incurs additional costs.
Power of Kanban
Kanban, often regarded as the jewel in Lean’s crown, is a visual management tool that facilitates the orchestration of work processes (work in progress or WIP). Originating from Japan, “Kanban ” means “visual signal.”
In project management, Kanban boards are the go-to tool. These visual boards represent workflows, tasks, and their statuses.
Each task is depicted as a card moved through columns representing completion stages. Team members can readily see what needs to be done, what’s in progress, and what’s completed.
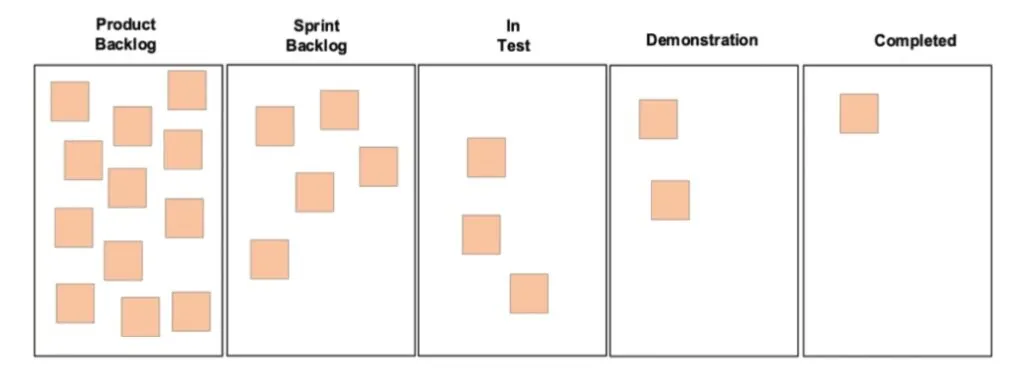
Understanding the workflow will go a long way in managing the work on a project. This work product movement is a metric for tracking the project’s progress
Practical Steps for Applying Lean in Project Management
Value Stream Mapping: Map out the entire project process to identify value-adding and non-value-adding activities. This helps eliminate Muda and optimize workflows.
Kanban: Use Kanban boards to visualize tasks, prioritize work, and maintain a steady project flow. Team members can see their responsibilities and the status of tasks, reducing confusion and inefficiencies.
Continuous Improvement: Foster a culture of continuous improvement within the project team. Encourage team members to identify and address issues as they arise, preventing the accumulation of waste over time.
Resource Management: Carefully plan and allocate resources based on their capabilities and capacity. Avoid overloading team members with excessive work to prevent Muri.
Standardization: Standardize project processes and documentation to reduce Mura. Clearly defined procedures help maintain consistency and predictability.
Feedback Loops: Establish regular feedback mechanisms to identify areas for improvement. Involve team members in the process to gather insights and make necessary adjustments.
Summary
Lean principles offer project managers a systematic approach to achieving efficiency, quality, and simplicity in their projects.
By eliminating waste (Muda), ensuring smooth flow (Mura), and avoiding overburden (Muri), Lean can significantly enhance project outcomes
References
Wikipedia article on Toyota Production System